- Sections :
- Crime & Public Safety
- Restaurants & Food
- Sports
- More
Solutions with Impact: The Top 4 Causes of Turnaround Delays
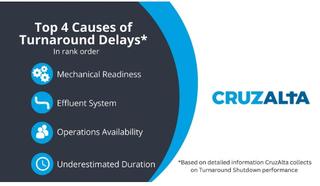
THE WOODLANDS, TX -- Turnaround failures are an unfortunate fact of life for many refineries, and no one wants to experience one. But what are the top causes of turnaround delays and how do you avoid them?
CruzAlta collects detailed information on Turnaround Shutdown performance. The top 4 causes of shutdown delays are (in rank order):
1. Mechanical Readiness
2. Effluent System
3. Operations Availability
4. Underestimated Duration
In this article, we’ll break down all four of those delays and discuss best practices for each.
Mechanical Readiness
The most common cause of turnaround delays is mechanical readiness.
Mechanical readiness for a turnaround includes having all the mechanical equipment, and facilities needed for shutdown, ready to go when needed. For example: hoses are laid out, temporary piping is installed and bolted up, temporary coolers/condenser/knockout pots are installed and connected, required temporary pumps are installed and ready to run, and (the most common deficiency) the temporary facilities are connected to the process piping, except where spools need to be dropped out for the connection to be made.
The best practice for making sure all this work is completed prior to feed out is to detail a comprehensive plan for all the installation of these facilities and load them into the TA Schedule file as pre-TA tasks.
Typically, this pre-TA scope is targeted to be completed 1-3 weeks prior to feed out and assigned to a dedicated mechanical crew to execute.
Effluent Management
Effluent management includes any deficiency associated with the facilities being used for handling the liquid effluent created during the shutdown steps. The most frequent scenario is when the system is hydraulically limited, which is typically the result of undersized temporary piping, a decision to not use temporary facilities to increase the capacity of permanent piping, effluent system overload due to unit sequencing changes, or inadequate system design (such as not installing temporary coolers or pumps). Occasionally, equipment failures and the presence of unplanned orifice plates occur, which fall within this category.
A best practice for effluent management is to develop a comprehensive shutdown plan that includes volumetric calculations, thorough walk-down of permanent facilities, frequent interactive contingency planning, and intense orientation of operators on the shutdown plan and procedure.
Operations Availability
Until recently, shutdown durations were typically not challenged and would represent the mentality around “what was proven last time.” The use of operators not qualified on the shutdown units is only recently being embraced, which further complicates the scenario. So effectively the shutdown duration was limited by the number of operators on the unit.
Over time, extreme focus on competitiveness revealed opportunities associated with shutdown duration reduction. This pressure resulted in operations teams reluctantly “giving up a few shifts or days,” but the number of operators required to deliver this faster shutdown was not studied. The industry is currently in the middle of this challenge and a few practices are emerging that are noticeably impacting this category of shutdown delay. Traditional TA scheduling tools are not designed to deal with tasks that can progress without people resources, and proven methods have been developed to effectively ensure the resources required to deliver the committed duration is known.
With the ability to understand the required number of operators, the industry is realizing that experienced contract operators, like those from the CruzAlta Operations Skills Team, can safely and effectively join the base operations team to deliver a faster shutdown duration.
Underestimated Duration
Underestimated Duration is the fourth most common cause of shutdown timeline extension. Unlike the first three reasons that we have been unpacked, the root cause of underestimating the shutdown duration is the failure to plan the shutdown effort in enough detail.
Historically, shutdowns were people intensive, and success was dependent on the heroic coordination of a few extremely experienced operations leaders. Procedures were in place, but mastering the fine details was atypical and challenging the shutdown duration was even more rare. Now that optimizing the shutdown window has finally been embraced as the most available turnaround event duration reduction opportunity, both experienced people and an extremely detailed shutdown program is essential.
“The Great Resignation” of the past three years has decimated the capability of most operations teams in our industry so dramatically that the historic people-dependent shutdown is not even an option. An aggressively optimized shutdown timeline is a prerequisite for delivering a competitive turnaround duration and requires an extremely detailed operations approach, one which is characterized by a collaboratively developed shutdown plan assembled by facility operations leads leveraging the experience of seasoned contract operations experts and an operations team aligned and committed to delivering the shutdown timeline. Without this comprehensive program, an aggressive shutdown target is not achievable, and shutdown duration extension will result.
At CruzAlta, we want to help our clients avoid these costly turnaround delays. It starts with a deep understanding of a client’s unique pain points, and we then apply a subset of our proven methodologies to address the specific site needs. We want our clients to think differently and confidently while experiencing operational excellence. Visit CruzAlta.com for more information.
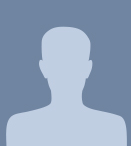